SPES 3U CubeSat Project
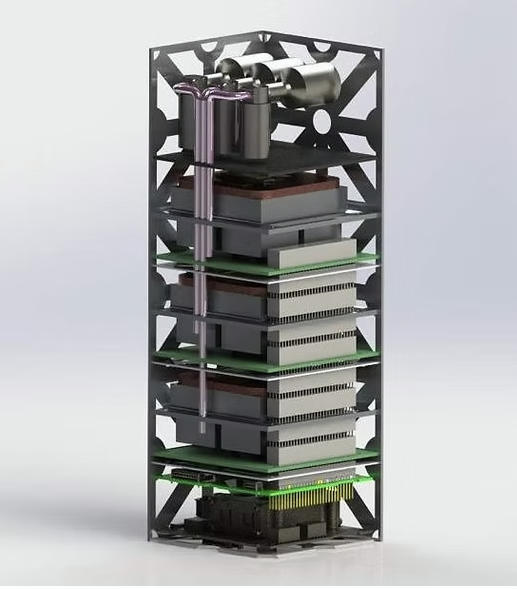
Date: 2020
SPES was a proposal for a 3U-CubeSat mission that was submitted to a worldwide competition initiated by The United Nations Office for Outer Space Affairs (UNOOSA) and Airbus Defence and Space GmbH. The objective of the mission was to develop a payload that could analyze and compare the structural behavior of three different types of bio-nanopolymers (BNCP) with the polymer (EVA), which is commonly used for space envelopes by NASA, in a microgravity environment. The SPES mission aimed to determine the potential of BNCPs as a potential replacement for conventional plastics in space.
The experimental set-up consisted of 3 Experiments (A, B, C) to test the Barrier Properties of two different BNCPs by measuring Water Vapor and CO2 Permeation Rates in a controlled environment of Temperature and Pressure.

The mechanical design of the CubeSat structure was made in Solidworks. The experimental set-up had 3 chambers (Figure 3) with four arrays each. Each array had pressure, humidity, CO2, and temperature sensors.
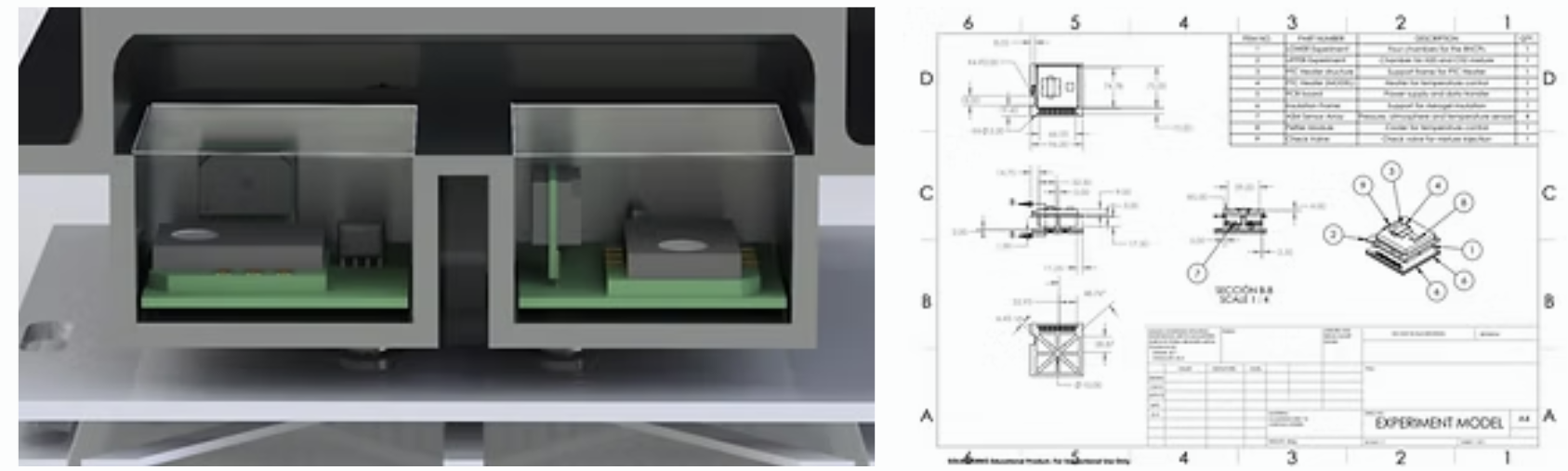
The payload structure was specifically designed to function effectively within a pressurized environment. The selection of materials was determined through the utilization of the GRANTA methodology, which encompasses four key pillars: objective, free variables, constraints, and function. Within this framework, the free variables were defined as the material and thickness of the structural components, while the constraints were based on the payload weight and volume. After a thorough evaluation, the Edupack software identified Aluminum 6061 T6 as the most suitable material for the payload structure. This decision was based on the software’s calculations that showed a graph of the slope between various densities and yield strengths of different materials (Figure 5) and a final function pointing out to Aluminum 6061 T6. Other several critical factors that further the selection of the material include its exceptional resistance to corrosion, outstanding strength-to-weight ratio, lightness, and machinability.
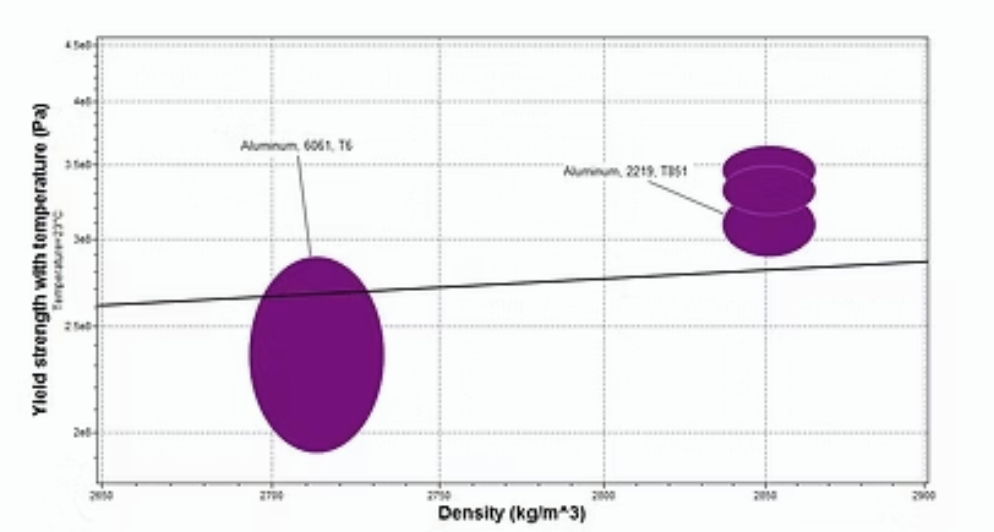
In terms of the design, a majority of the structural components exhibit a safety factor exceeding 2. This indicates that each element of the payload is capable of withstanding the rigorous conditions of space, as well as external loads, without encountering any significant risk of damage or necessitating further redesign. Moreover, the chassis design of the payload was developed utilizing the strength distribution theory, which guided the selection of an isogrid pattern on the payload walls (Figure 6). This pattern was specifically chosen to minimize stress points and to reduce overall weight.
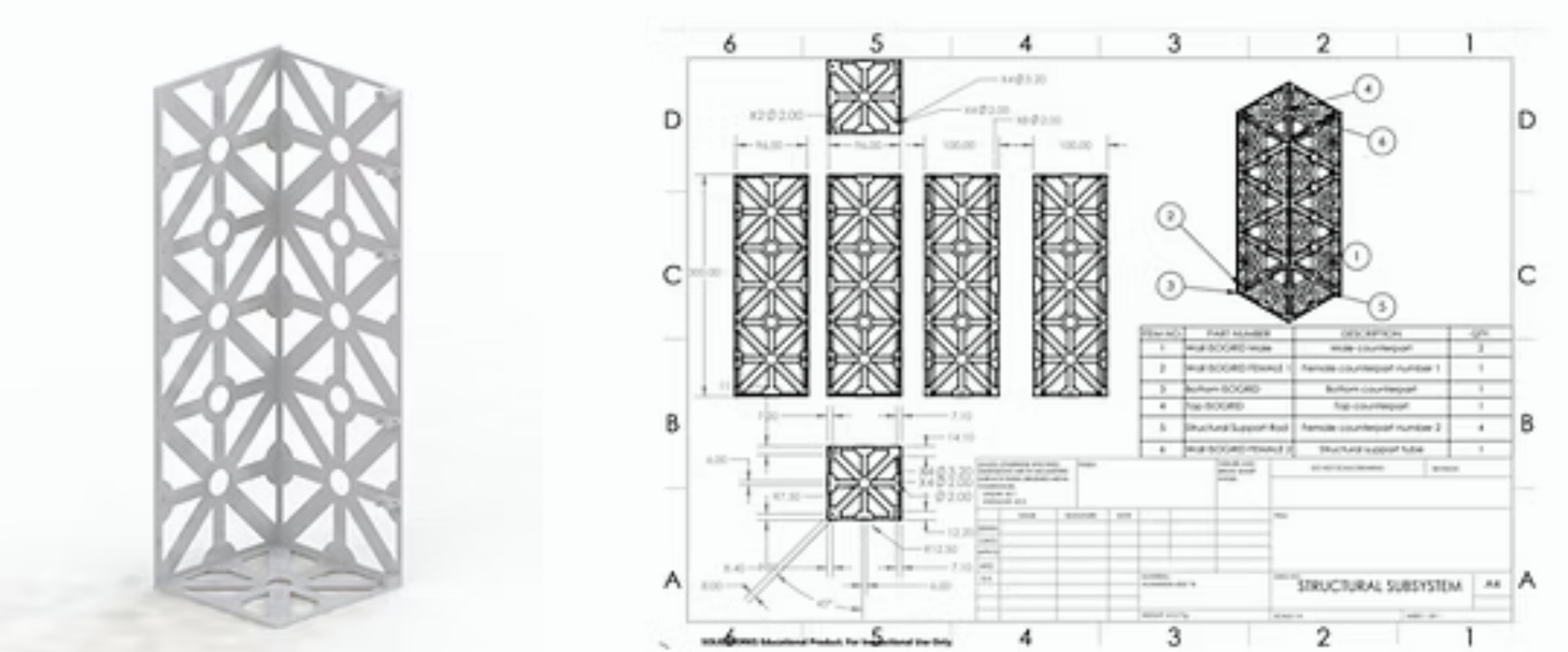
Finally, stress concentration simulations were made. Considering the results, the team concluded that the maximum stress suffered by the components of the payload during launch will be approximately 1.33MPa. And the deformations will not exceed 1.687x10-3mm.
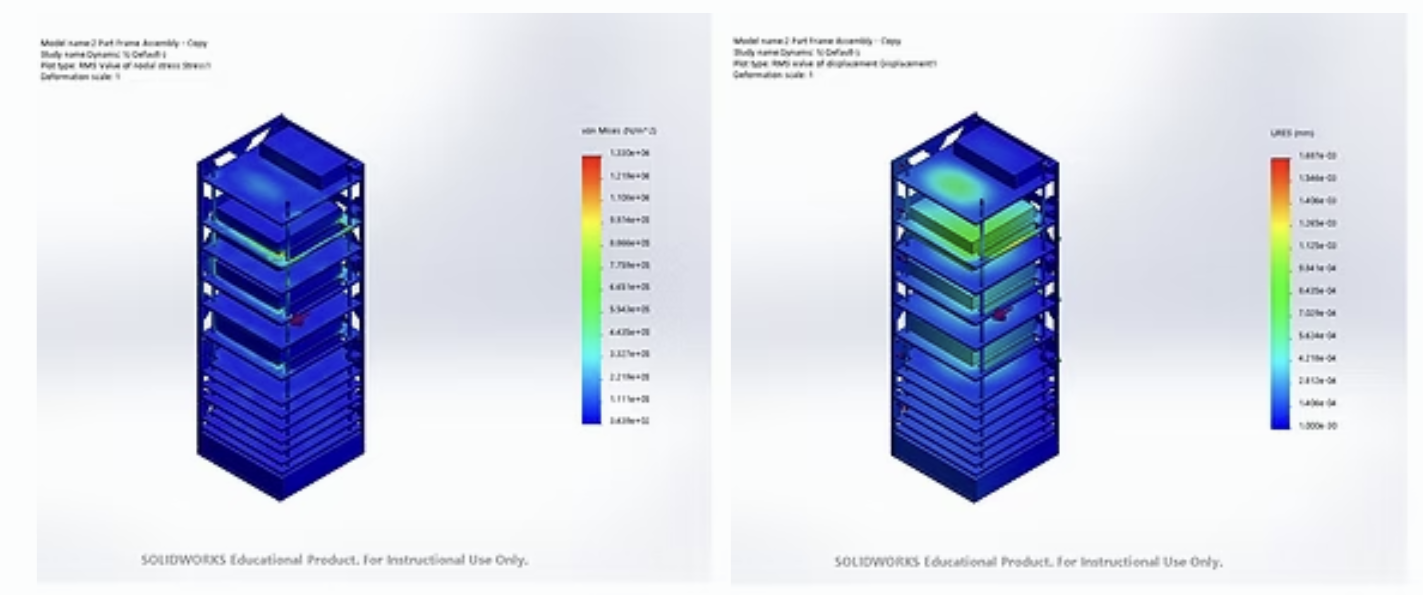