Pressure Regulator for Organ-On-a-Chip
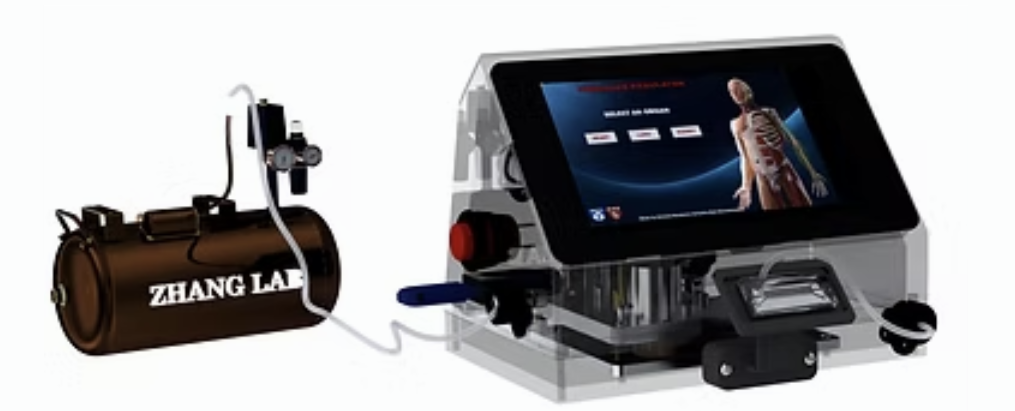
Date: 2021
The pressure regulator is a cost-effective device designed to modulate and mimic an organ's given pressure signal, provided by a USB image graph, onto an organ-on-a-chip(OOAC) platform. Combining the pressure regulator with an OOAC forms a comprehensive system that seeks to replace traditional animal testing procedures with more effective and ethical in vitro models.
The design was based on three main factors:
- Cost-effectiveness: The common pressure regulators on the market cost around 1000USD or higher, compared to the one developed at the laboratory which cost around 300USD. The material utilized for the structure was PLA and the rest of the components were purchased from different electronic websites.
- Precision and accuracy: In order to ensure the precision and accuracy of the system, a key consideration was the design of the structure itself. This involved taking into account the number of inlets and outlets required by the microfluidic system inside the organ-on-a-chip platform and the material used in the structure's construction, tolerances, and accommodation for external components. To develop the model, Solidworks was used, and each render was made using Visualize Content. In addition, Geometric Dimensioning and Tolerancing (GD&T) was applied to all drawings to improve quality and avoid errors when manufacturing. The overall design consisted of both external and internal parts. The external component was the outer case, which housed the display and the organ-on-a-chip platform (Figure 1). This structure was 3D printed using PLA on an Ender 3. The internal component, on the other hand, was composed of proportional solenoid valves with their respective 3D printed holders, air tubes, a PCB with screw fixing supports, and a pressure sensor (Figure 2). The organ-on-a-chip platform, made of PDMS, features specific orifices, including two dedicated to the valves and one for medium circulation. These features were carefully considered in the design process to ensure optimal functionality and performance of the overall system.
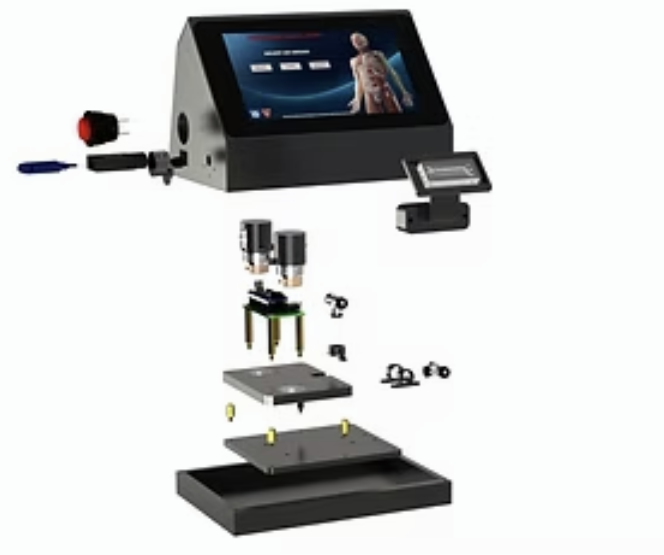
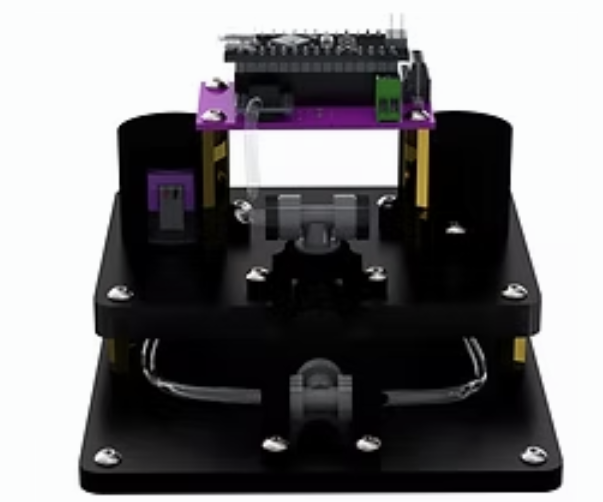
In order to provide optimal stability to the system, it is necessary to maintain precise pressure control over the proportional solenoid valves. To achieve this, a Proportional-Integral-Derivative (PID) controller was implemented to modulate the current and precisely regulate the valve opening. One valve was designated for airflow, while the other acted as an exit for normalized pressure. Real-time pressure measurements were continuously taken to further enhance accuracy and control.